Protective Coating to Prevent Corrosion of Steel Structure – A Need-Based Approach
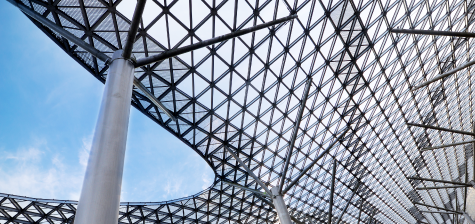
Structural steel is widely preferred by engineers because of its strength, ductility, availability, ease of fabrication to the desired geometry, quick erection, and reusability. Beautifully designed and aesthetically pleasing buildings, memorials, bridges, towers etc all over the world bear testimony of the wonders that a steel structure can create.
According to a report by one of the market research groups, the demand for structural steel shall be US$ 226.91 billion by 2030 growing at a CAGR of 6.3% from US$ 123.5 billion in 2020.
Source: www.precedenceresearch.com
The primary reason for the growth in demand is attributed to large-scalable urbanisation and growth in infrastructures. A major drawback of steel construction is corrosion resulting in higher maintenance costs. Hence, the responsibility of a structural engineer is not confined to the economy, safety and aesthetics alone but durability and sustainability as well.
Structural designers walk a very tight rope in balancing between the durability and cost of the structure. While corrosion is bound to happen under relevant exposure, protective coating is costly at the initial stage and during the life cycle also. Further, embodied energy is very high in the paint and paint manufacturing is a carbon-intensive process. Hence, possible means to reduce the consumption of paint is an important feature towards embracing a carbon-neutral economy by 2050 in line with the Paris agreement (COP21).
In addition, paint application and its satisfactory performance demand appropriate surface preparation which consumes additional cost and energy. American Institute of Steel Construction (AISC) in its Technical Advisory has recommended doing away with paint of enclosed structures when humidity is less than 70% and/or it is not exposed to chemical attack. Barring severe exposure, designers need to adopt an alternative to protective coatings or steel treatment that would provide better cost-effective steel structures during the life cycle. There are stipulations of providing sacrificial thickness in the form of corrosion allowance in the standards of some special structures like stacks, bunkers and silos to mitigate corrosion and abrasive actions of the material.
It is evident that optimisation of the steel structure without compromising safety and durability requires insight and understanding of the exposure and the mathematics of corrosive effect. ISO 9224 – “Corrosion of metals and alloys – Corrosivity of the atmospheres – Guiding values for the corrosivity categories” provides guiding values of corrosion attack for metals and alloys exposed to natural outdoor atmospheres for exposures greater than one year. These values for standard structural materials can be used for engineering calculations. The guiding corrosion values specify the technical content of each of the individual corrosivity categories for these standard metals.
The rate of corrosion exposed to natural atmospheres does not remain constant and gradually reduces over time as the corrosion products deposit on the metal surfaces. A Formulation for loss of mass of the metal or depth of corrosion has been made based on the nature and duration of exposure. Designers need to adopt the good practice of assessing the extent of corrosion and determining the coating requirements. It is quite probable to observe that the margin provided during structural design is enough to compensate for the corrosion loss and thus costly coatings from the perspective of providing protection against corrosion could be avoided. It is a common practice of providing a coating system for structures under normal atmospheric conditions based on the longevity of the life of the coating rather than the actual requirements from the assessment of corrosion loss. A sample calculation is appended to illustrate how an element designed structurally can serve the design life without undergoing any protective coating.
Let us consider a simply supported beam with compression flange restrained and subjected to maximum factored moment 190 kN-m and shear force 152 kN. Design life shall be 20 years and the atmospheric corrosivity is C5 as per Table 4 of ISO 9223 signifying very high corrosivity. Grade of steel E250. Beam shall be designed as a plastic section corresponding to Class 1 of IS 800: 2007.
Selection of suitable section:
Let us built-up a section having a depth of web 350 mm and a flange width of 150 mm. Now, minimum thicknesses of web and flange required from strength and serviceability shall be determined as:
e = (250 / fy) 0.5 = 1
From Table 2 of IS 456: 2000, to make the section plastic
d / t < = 84 e, Therefore minimum thickness of web = 4.17mm
b / t <= 8.4 e, Therefore minimum thickness of flange = 8.7mm
Minimum Section size satisfying strength and serviceability is determined by trials as shown in the Table below.
Trial | Flange thickness (mm) | Web thickness (mm) | Check for Shear | Check for Deflection | ||||
Design shear (kN) | Shear capacity (kN) | Remark | Actual deflection (mm) | Permissible deflection (mm) | Remark | |||
1 | 10 | 6 | 152 | 275.55 | SAFE | 13.86 | 16.67 | SAFE |
2 | 10 | 8 | 152 | 367.4 | SAFE | 13.07 | 16.67 | SAFE |
3 | 10 | 10 | 152 | 459.26 | SAFE | 12.37 | 16.67 | SAFE |
Trial | Flange thickness (mm) | Web thickness (mm) | Design Moment (kN-m) | Is Cl. 8.2.1.2 applicable | Check for Moment | ||
Plastic Modulus required (cm3) | Plastic Modulus of the section (cm3) | Remark | |||||
1 | 10 | 6 | 152 | Yes | 833.228 | 723.75 | UNSAFE |
2 | 10 | 8 | 152 | Yes | 833.228 | 785 | UNSAFE |
3 | 10 | 10 | 152 | Yes | 833.228 | 846.25 | SAFE |
From above, the minimum flange and web thickness are both 10 mm.
Assessment of corrosion allowance as per ISO 9224
According to ISO 9224, the value of long-term corrosion loss can be determined as,
D(t)= rcorr tb
Where, D = corrosion depth [mm], t (in years) is the exposure time & rcorr is corrosion rate in the first year of exposure in micrometres per year (mm /a).
b is coefficient for metal-environmental-specific time exponent, usually less than 1.
For a structural steel member with a design life of 20 years, the depth of corrosion may be assessed based on the above formula.
For a corrosivity category of C5 (refer to Table-4 of ISO 9223), corrosion rates, rcorr for the first year of exposure for carbon steel material is considered between 80 to 200 mm /a.
A corrosion rate of 2be mm /a is considered.
In accordance with ISO 9224 Clause-5, for the prediction of corrosion attack after extended exposure, an appropriate b value is selected according to clause-7. In cases where the detailed composition of the metal is not known, B1 the value provided in Table-2 of ISO 9224 shall be adopted. This value of B1 shall be considered as the b value and to be used in the equation for predicting long-term corrosion loss.
b value is considered as 0.523 as per ISO 9226 clause-7, Table-2 for carbon steel.
D (20 years) = 200 * (20) ^0.523 = 958 mm = 0.96 mm
Hence, it is observed that margins in both the thicknesses available in flange (10-8.7) = 1.3 mm and web (10-4.17) = 5.83 mm are higher than the estimated corrosion loss of 0.96 mm over the design life. Therefore, providing an expensive protective coating corresponding to high atmospheric corrosivity may be dispensed with and instead a normal coating for aesthetics would serve the purpose.